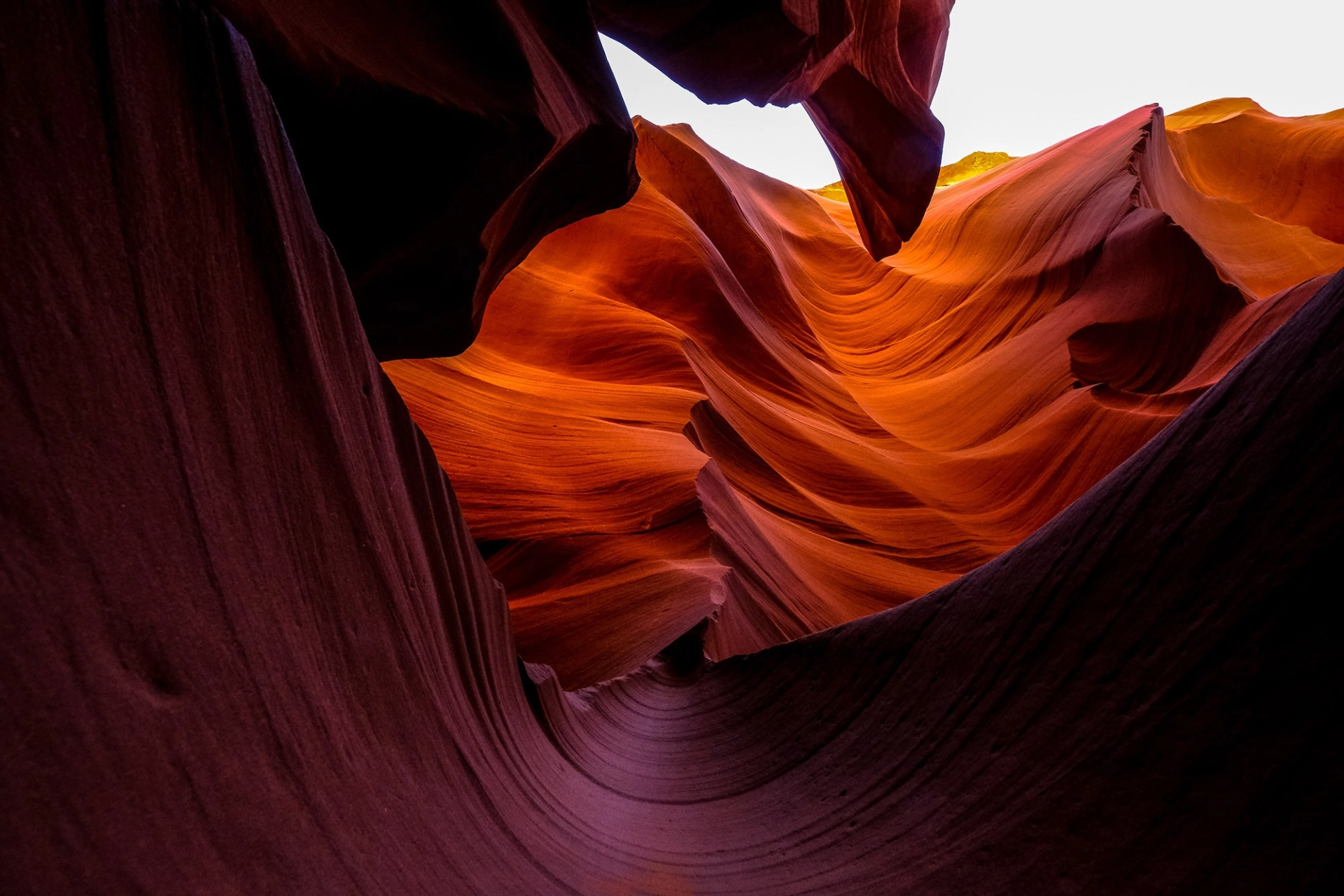
43rd OESAI Annual Hybrid Conference
Aon South Africa
With trade already heavily challenged by the COVID-19 pandemic, the current wave of riots and looting in parts of the country is exacerbating matters further, presenting a tipping point for many businesses as to whether they survive or not. The violent and destructive protest action of the last few days has thrown supply chain risk into stark contrast yet again, with businesses scrambling to secure the weak links, safeguard lives and property and reduce the risks to business continuity as far as possible.
“As a result of the pandemic, there has been a major consumer shift to online shopping with people clicking a button on their computer and getting goods delivered to their home. With so much of the supply chain happening behind the scenes and out of sight, consumers generally do not understand the complex and interlinked processes involved in getting that parcel or service delivered to their doorstep,” explains Tony Webster, of insurance brokerage and risk advisors, Aon South Africa. “It’s only when something goes horribly wrong, as it has in the last few days, that there is a realisation of just how critical, yet fragile supply chains are, and how the domino effects of an incident reverberate throughout the entire value chain,” Webster adds.
Why it matters
With major highways and byways in and out of KZN blocked, it means that tens and thousands of fleet vehicles are unable to deliver goods across the country from South Africa’s busiest port, not to mention delays caused in Gauteng, the country’s economic hub. Goods will be late in reaching destinations, if at all, as transport operators run the risk of having trucks and cargo damaged, burnt or looted by rioting crowds.
It is not uncommon for multiple events that disrupt supply chains to occur simultaneously.
“It’s quite possible that certain providers of products are going to be caught up in more than one event concurrently, as these events rarely wait for each other to finish and do not operate in a linear way,” says Webster.
In addition to the disruption of business operations, the impact of breakdowns in logistics systems raises another peril: reputational risk.
“Because consumers rarely separate the logistics from the provider of the product, the business involved could be hit twice: an immediate impact on revenue and profit, along with a loss of attraction in the future triggered by reputational damage. We’ve all been lulled into believing that everything is a click away and that’s fine if it works, but it only works when that specific supply chain is absolutely fluid and nothing goes wrong,” Webster explains.
It falls on the businesses whose products, essential components or raw materials are in the supply chain to evaluate and address these risks and put measures in place to mitigate them.
“Whatever businesses are producing or manufacturing, they will have a portfolio of products, and some of those products will be more valuable than others, either because they generate more income or because they service a market that’s growing for them or they are crucial for a key customer,” says Webster. “If they understand what’s driving the value of that business, they can then start to find the potential supply chain pressure points and risks around the end-to-end fulfilment of that product.”
Businesses should identify their most crucial supply chain ecosystem and the suppliers that are critical to that ecosystem. How a company addresses the risk becomes clearer once the points where a blockage or incident could negatively affect its ability to deliver products or services have been identified. Then they can ascertain their course of action, whether it is to hold more inventory, bring suppliers closer to home, diversify distribution points geographically, explore new logistics options or other alternatives.
“We’re seeing companies start to think more strategically around the business continuity element,” says Webster. “It’s all about how an organisation fulfils its most important client needs if a portion of stock is lost, which may mean relying on redundant supply, using a different route or other alternatives.”
Reshaping organisational response strategy
In addressing risks identified during the ongoing pandemic, many organisations made changes to their operating models, workforce strategies, products, portfolios, supply chains and more. The pandemic has created massive uncertainty, but also an unprecedented opportunity to learn and reshape parts of an organisation, building resilience for future shocks.
Concerns over geopolitical tension have been simmering in the background for a while and with domestic political unrest front and centre on South African soil at present, organisations are bound to find out just how resilient these changes are in the face of major disruption to their supply chains.
“It is at times like these where the insights and advice from experts in the field prove to be invaluable. Defining the fine line between what organisational risks can be handled internally and what aspects of that risk need to be covered externally, will provide a roadmap amid massive uncertainty,” concludes Webster.